Challenge & Context
The scenario is focused on the quality of the welding process in truck manufacturing. The welding process is a crucial step in the automotive industry, since it has a high impact on the subsequent processes and the final quality of the product. In fact, defects occurring in the welding cell, if not correctly detected, could be propagated in the painting process, assembly process or the final inspection, resulting in either the reworking or discarding of the car body, hereby increasing the production time and cost.
The developed solution allows for continuous monitoring of the parameters related to the welding process and makes use of data analysis algorithms, in order to detect unexpected parameter behaviour or to optimize the planning of special maintenance interventions, based on historical data, enabling a Predictive Maintenance (PdM).
In further detail, the following challenges and bottlenecks are addressed:
- The machine saturation needs to be maximized, impacting the number of jobs per hour and the total throughput.
- Unexpected maintenance intervention could be required to bring a machine in optimal working condition, avoiding or reducing line stops, causing delays in production, the need for rescheduling and, as a consequence, additional costs.
- The request for urgent intervention by the maintenance service supplier reducing additional costs.
- There is no advice in case of potential future problems and abnormal parameter trends reducing additional costs.
- The data analysis is not executed in real time but delayed. In this way, immediate problems can’t be detected and handled in time.
- Reparation and rework lead to a waste of materials and additional operations reducing additional costs.
The solution permits the user to monitor the plant and identify events in real time, take preventive decisions and understand the impact of events on the plant economics (saturation of machines, throughput, and so on).
Solution
The designed solution aims to reduce defects in the automotive manufacturing process. It is based on Open Source components, allowing for a faster and simpler adoption, meeting the needs of enterprises. The Reference Architecture is able to gather data from common devices and industrial machines, allowing for easy integration, supporting common industrial standards and interfaces (e.g. OPC UA, MQTT, etc.), and providing a platform for data visualization and monitoring in order to discover trends and understand, in advance, possible abnormal behaviour.
Furthermore, the solution is compatible with existing open components for data brokering aiming to integrate industrial platforms that are already in place, making it suitable for short time adoption (SMEs barriers).
Another important aspect is the integrability with proprietary platforms such as Siemens MindSphere, the Industrial IoT (IIoT) platform powered by Siemens and adopted by many large enterprises.
On the one hand, the CPS/IoT Industry 4.0 platforms and solutions need to be connected to the real scenarios experienced by industrial plants and connected factories. This often implies that decisions must be taken in the short term (near real time) and locally on a set of data which is constantly growing bigger and more complex. Cloud architectures are usually well suited for many application domains, but often reveal some limitations when applied to Industry 4.0 scenarios.
Similarly, the adopted solution addresses both greenfield developments, and brownfield integration, as well as interoperability with proprietary solutions and standards. This aspect is very important especially when a new platform needs to address a market, which is already covered and saturated by big IT players. Brownfield integration is, in this case, a must and needs to be implemented in an open and interoperable way.
The FIWARE Reference Architecture for Smart Industry, compliant with existing industry architectures such as the Reference Architecture Model Industrie 4.0 (RAMI4.0), the Industrial Data Space Reference Architecture or the Industrial Internet Consortium Reference Architecture, enables the digital transformation. FIWARE is an Open Source solution providing developers with maximum agility and flexibility and offers something similar to building blocks, defining the size and orientation of the studs to ensure that all the different types of blocks join together.
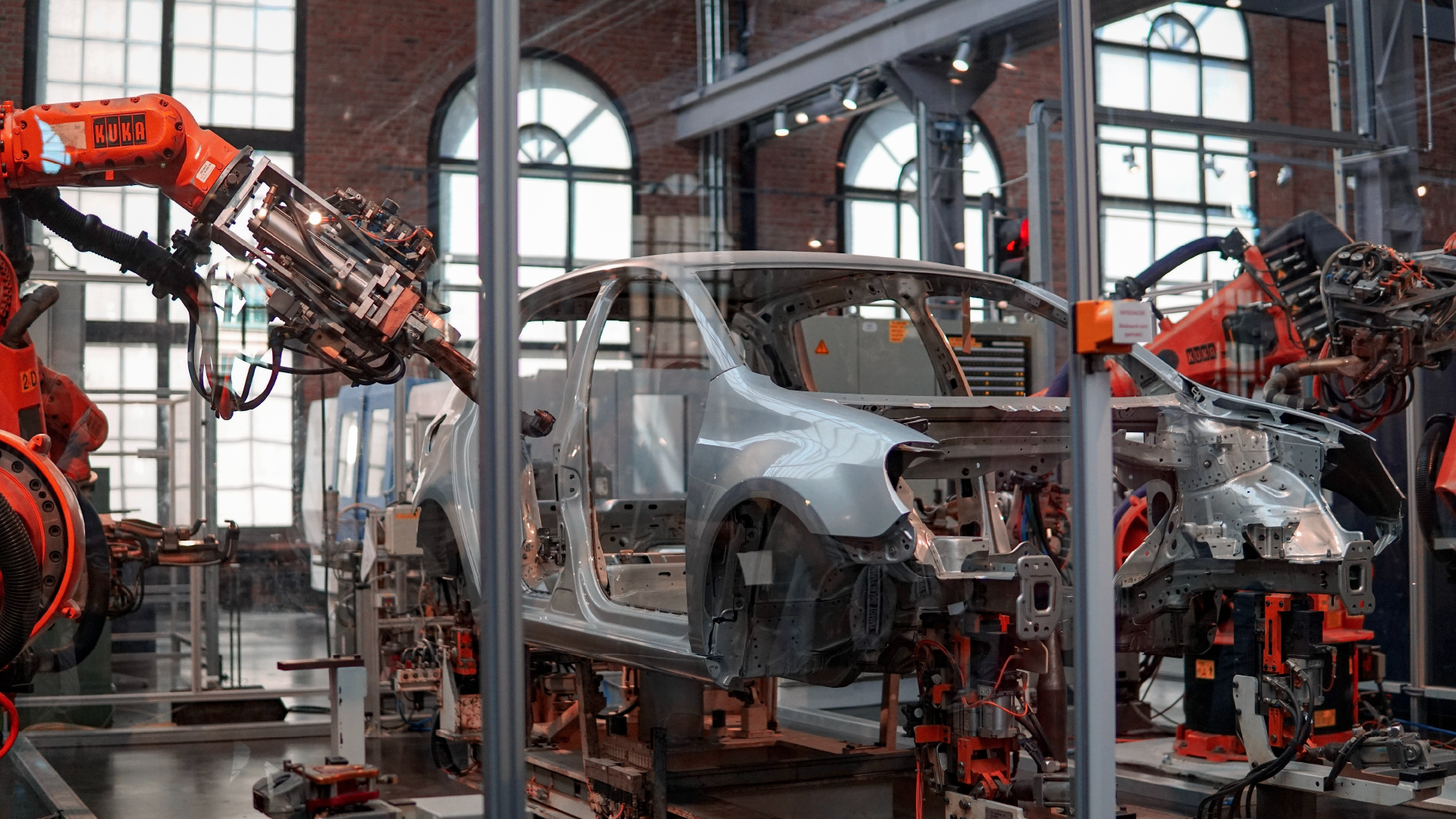
How it works
In the AUTOMOTIVE SMART FACTORY use case, FIWARE components are able to describe the entire data chain, from the collecting by custom connectors, through the processing of data from the plant. The solution is supported by an open platform aiming to be easily integrated with existing devices and platforms. The solution is able to process:
- Situational Data from the environment context (i.e. weather data, traffic data, etc.).
- Data in Motion is in fact generated by different real-world assets in the Smart Factory (machine tools, robots, warehouses, human workspaces) or in the Smart Product (fleet of vehicles, product service systems, smart objects).
- Data at Rest needs to be processed in order to feed AI-based advanced applications in the field of factory and product condition monitoring, health diagnosis, predictive maintenance, zero defect quality, energy and waste management, human-machine interaction, etc.
Only by making use of FIWARE components, the Platform is able to collect data coming from different IIoT devices. The data gathered is managed using the IDAS framework (e.g. supporting OPC UA, MQTT, LORAWAN, etc.) and can be extended with custom connectors. Furthermore, the FogFlow components offer Edge Computing capabilities, providing new features such as local data processing, reducing the number of messages between the IoT device and the cloud, since the data provided by sensors can be pre-processed, aggregated, privatized. In turn, it results in network decongestion, increasing data processing speed and security.
Data is collected by the Orion Context Broker using NGSIv2 as a data model. On the brokering level, the platform is integrated with Siemens MindSphere, a cloud-based, open Internet of Things (IoT) operating system that enables industries worldwide to link their machines and physical infrastructure to the digital world in an easy, quick and economically attractive way.
Moreover, the solution platform integrates a mechanism for interoperability with Apache components, a connector (the FIWARE-DRACO components) in charge of persisting context data into third-party databases and storage systems, creating a historical view of the context. Internally, FIWARE-DRACO is based on Apache NiFi (Niagara Files), an Open Source software that automates and manages the flow of data between systems.
Data can be processed from the Perseo component (Complex Event Processing engine) and stored using the FIWARE Persistence Layer (i.e. Draco, Cygnus, etc.). Finally. Equally, data can also be consumed with the FIWARE Visualization Layer (i.e. KNOWAGE) creating a custom dashboard to visualize and monitor data.
The architecture depicted in Figure 1 is the MIDIH Open Platform Architecture composed mainly of two lanes (FIWARE and APACHE) in order to support many industrial scenarios (i.e. Smart Factory, Smart Product, etc.).
The green blocks are deployed to support the automotive landscaping, gathering data directly from industrial machines and from IT systems. The Orion Context Broker acts as a data broker. Data are persisted using Cygnus and consumed with Wirecloud and KNOWAGE components, creating customized dashboards.
Figure 1 . Use Case mapping toward the MIDIH Open Platform Architecture
Benefits & Impact
- Number of users: 1–100
- Expected users looking at the future: Data Managers
- Customer: FIAT, Centro Ricerche Fiat
- Number of new potential clients: 1/100
- Investments, savings, efficiency growth expected etc. in 3 years:
– 20–30% decrease in costs for the management of unpredicted maintenance events reduction
– 5% increase in Mean Operating Time Between Failures (MTBF)
– 0.5–1% OEE increase
– 5–10% decrease in low quality bodies
Which target group will see the highest impact and why?
Large enterprises can enrich their systems by integrating data coming from the FIWARE platform. Furthermore, SMEs can benefit from the FIWARE ecosystem, putting in place an open platform able to cover the entire data chain.
Why is this solution / project important to the company, city, society etc.?
Discovering trends allows for an awareness of patterns that can be monitored in the future to intercept potential anomalies. Predictive maintenance needs to be fed by rules based on historical data, learning from the past to improve the process. The platform is based on Open Source components representing a fast-adoption solution in the IIoT environment.
Added value through FIWARE
The Platform part of this solution enables data processing on the edge, reducing latency and increasing the process performance. Thanks to its modular and flexible nature, the platform can easily be extended to cope with both greenfield and brownfield integration scenario.
The FIWARE Open Source approach allows for an Open Source solution that covers the entire data flow, from sensor data acquisition to data visualization. Also, the FIWARE Architecture for Smart Industry represents a fast-adoption solution breaking down SMEs barriers. Moreover, FIWARE supports the main industrial standards and can easily be integrated with other open platforms (i.e. Apache components) and commercial platforms (i.e. Siemens MindSphere) making it attractive for large enterprises.